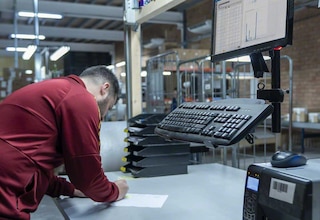
L'amélioration continue et ses applications en logistique
L'amélioration continue vise à augmenter la qualité et les performances d'un produit ou d'un processus par une analyse permanente des éléments impliqués. Cette technique, d'origine japonaise, est de plus en plus populaire parmi les entreprises occidentales. L'amélioration continue garantit de meilleures performances grâce à des changements mineurs mais continus visant à éliminer les habitudes peu productives et à normaliser les règles.
Dans cet article, nous expliquons le concept d'amélioration continue, ses principales stratégies et ses applications au secteur logistique.
Qu'est-ce que l'amélioration continue ?
Les techniques d'amélioration continue sont un ensemble de stratégies visant à perfectionner et optimiser les procédures, les produits ou les services par des ajustements mineurs, résultant d'une connaissance approfondie des opérations, et de l'analyse des données.
Il existe de multiples méthodes s'appuyant sur la stratégie d'amélioration continue pour développer les performances d'une installation logistique. Cependant, la méthode Kaizen ou méthode des 5S est devenue l'une des plus populaires en raison de sa simplicité et son efficacité.
L'amélioration continue par le Kaizen
Le Kaizen (terme japonais qui veut dire « s'améliorer à travers le changement ») est une méthode développée par l'ingénieur japonais Taiichi Ohno pour le constructeur automobile Toyota après la fin de la Seconde Guerre mondiale. Sa fonction était d'augmenter la compétitivité de la marque et de l'égaler à celle des constructeurs américains. Cependant, ce concept est aujourd'hui devenu une norme en matière de gestion d'entreprise à l'échelle mondiale.
La méthode Kaizen repose sur le principe qu'il est toujours possible d'améliorer un processus même s'il remplit correctement sa fonction. Appliquée surtout à la production et à la logistique, cette stratégie utilise un ensemble de procédures pour analyser le fonctionnement de l'entreprise, détecter les manques d'efficacité et mettre en œuvre des changements. Le tout tourne autour de cinq principes, connus sous le nom des 5S en raison de leurs noms japonais d'origine :
- Seire (le tri) : le premier processus de la méthode Kaizen consiste à passer au crible les tâches pour distinguer celles qui apportent une valeur ajoutée au produit ou au service (ces tâches sont dénommées gemba).
- Seiton (l'ordre) : l’employé doit avoir à sa disposition tous les outils lui permettant d'être agile et productif. L'application de Seiton consiste à organiser des équipes de travail pour éviter les déplacements ou gestes inefficaces.
- Seiso (le nettoyage) : l'identification des défauts et le nettoyage du lieu de travail sont essentiels pour que l'opérateur soit à l'aise et travaille au maximum de ses capacités.
- Seiketsu (la standardisation) : après identification des défauts, il faudra établir les règles ou procédures nécessaires pour augmenter l'efficacité des processus.
- Shitsuke (la discipline) : cette dernière étape est fondamentale pour la réussite des quatre précédentes. Elle implique un engagement de toute l'organisation à internaliser les nouvelles règles et à adopter une philosophie d'amélioration continue pour augmenter la valeur des opérations.
En somme, la méthode Kaizen par les 5S est une stratégie idéale pour augmenter la rentabilité de votre organisation, identifier et éliminer tout manque d'efficacité et, surtout, développer toute source de valeur.
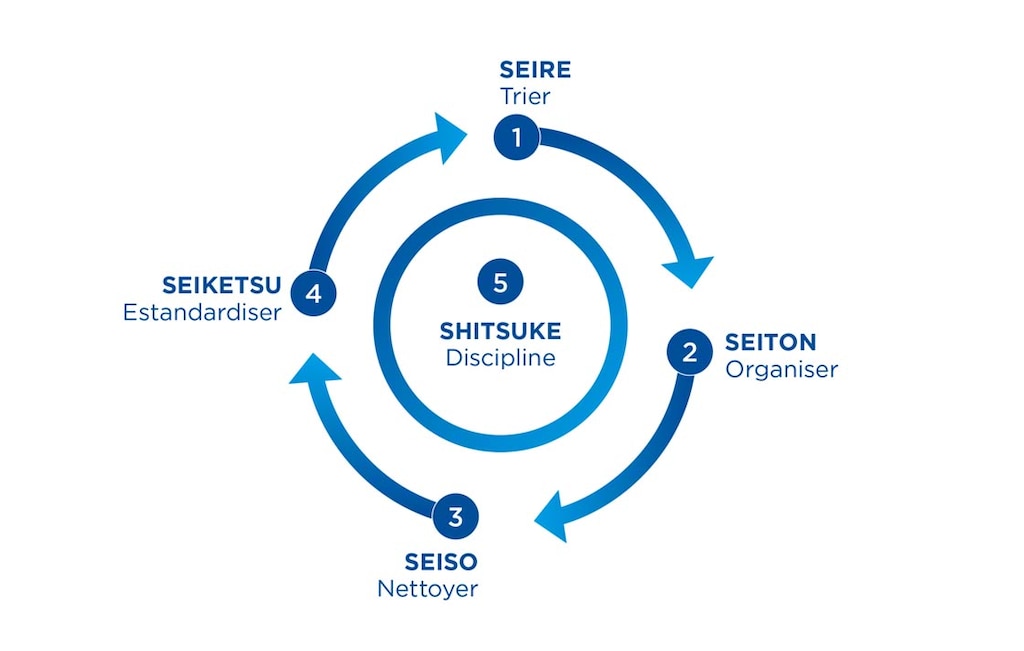
Autres méthodes d'amélioration continue : du PDCA au Six Sigma
En plus de la méthode des 5S, il existe d'autres stratégies et outils applicables à l'amélioration continue. Leur priorité étant d'atteindre l'excellence dans les processus grâce à l'information générée. Ci-dessous d'autres méthodes importantes de normalisation de l'amélioration continue :
- Le cycle de Deming ou PDCA : PDCA est le sigle anglais pour 'Plan, Do, Check, Act'. Cette stratégie cyclique décrit les quatre étapes essentielles pour détecter les manques d'efficacité, planifier des solutions et finalement améliorer la rentabilité des processus de l'entrepôt.
- Le Six Sigma : cette technique d'amélioration continue consiste en la suppression des erreurs lors de la livraison du produit final au client. Son objectif est d'atteindre 3,4 erreurs au maximum par million d'opportunités, où on entend par erreur toute incidence susceptible de provoquer l’insatisfaction du client.
- La méthodologie Lean : la stratégie Lean est basée sur l'identification de toutes les étapes qui n'apportent pas de valeur ajoutée au produit final afin d'obtenir un produit de la plus haute qualité.
Pour mener à bien une amélioration continue, il n'est pas nécessaire de faire un choix parmi les différentes méthodes, car aucune méthode n'est meilleure que l'autre, elles sont complémentaires et chacune d'entre elles a ses avantages. Toutes les stratégies peuvent et doivent être appliquées simultanément. L'objectif est de toujours s'améliorer : réduire les manques d'efficacité, introduire des changements progressifs et veiller à ce que les nouvelles habitudes soient bien adoptées au sein de l'entreprise.
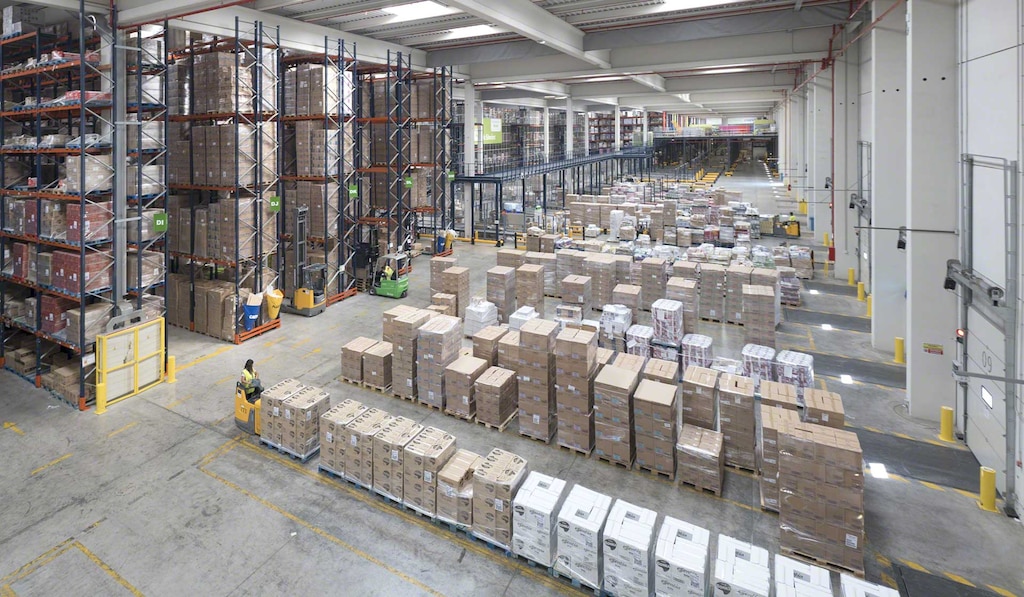
Le gaspillage : muet, mura, muri
Les techniques d'amélioration continue comprennent l'analyse permanente des processus pour assurer une rentabilité maximale à chaque étape. Par exemple, les termes muda, mura et muri englobent une stratégie visant à identifier les erreurs et le gaspillage en production.
Ce système, également connu sous le nom des 3M du Système de Production Toyota, est basé sur l'analyse des erreurs et des pertes d'un processus de production pour pouvoir, à travers de changements dans l'organisation, produire sans défauts et garantir la meilleure expérience au client. Voyons ces trois concepts clés :
- Muda (gaspillage) : ce sont les erreurs qui consomment des ressources et n'ajoutent pas de valeur au produit. À l'origine, la méthode de Toyota intégrait 7 pertes courantes dans une usine de production : les déplacements inutiles, les stocks excédentaires, les retraitements (opérations répétitives), la surproduction, le temps mort entre les lignes de production, les surtraitements (des procédures ne créant pas de valeur) et un transport inefficace.
- Mura (irrégularité) : le responsable de la production doit détecter tout déséquilibre, interruption ou changement de la charge de travail entraînant un surcoût de production. Cela nécessite un contrôle exhaustif des performances des processus de production afin d'identifier les défauts, les erreurs ou la non-exécution. Comment régler ces irrégularités ? En mettant en œuvre des méthodologies d'alignement de la production sur la demande, comme la méthode Kanban ou le just-in-time.
- Muri (surcharge) : l'ensemble des types de perte formé par le muda et le mura (gaspillage et défauts) provoque ce que les japonais attribuent à muri, à savoir le stress. Une mauvaise planification entraîne la fatigue des opérateurs, voire des goulots d'étranglement au niveau des lignes de production.
En bref, en appliquant la méthode des 3M de Toyota pas à pas, on élimine les gaspillages dans la production et, les perturbations et déséquilibres de la charge de travail. L'élimination à la fois du muda et du mura entraîne ainsi l'éradication du muri, c'est-à-dire du stress et de l'instabilité dans les lignes de production.
Les avantages de l'amélioration continue dans l'entrepôt
Comment l'amélioration continue de l'activité logistique et du quotidien de l'entrepôt peut-elle vous aider ? Voici les principaux avantages :
- La garantie d'un produit/service de qualité : la mise en œuvre d'une technique d'amélioration continue assure le succès de la production ou de la logistique, ce qui implique une meilleure expérience pour le client final.
- La réduction des coûts logistiques : cette stratégie permet d'optimiser les stocks de l'entrepôt, de réduire le lead time (délais de livraison) des fournisseurs, de donner la priorité aux opérations les plus productives et de supprimer celles n’en créant pas.
- Des déplacements utiles : les méthodes comme le Kaizen ou le PDCA éliminent les déplacements inutiles et proposent des itinéraires de picking plus efficaces, garantissant ainsi une meilleure productivité des opérateurs.
En plus de ces améliorations, la mise en œuvre de ces systèmes facilite l'intégration d'un état d'esprit de type « pull flow » dans les installations. Cela veut dire que les procédures de l'entrepôt fonctionnent selon le principe du JIT (just-in-time), où les tâches sont exécutées lorsqu'il y existe une demande du client, évitant les opérations inefficaces et les risques de sur-stockage ou l'obsolescence des marchandises.
Mecalux dispose de multiples solutions pour accompagner la mise en œuvre d'une méthode d'amélioration continue telle que le Kaizen ou le PDCA. Supply Chain Analytics, le module avancé d'Easy WMS, permet au responsable logistique de collecter toutes les données de l'entrepôt et de structurer ces informations pour créer des KPI logistiques pertinents et mesurer l'impact de la stratégie d'amélioration continue.
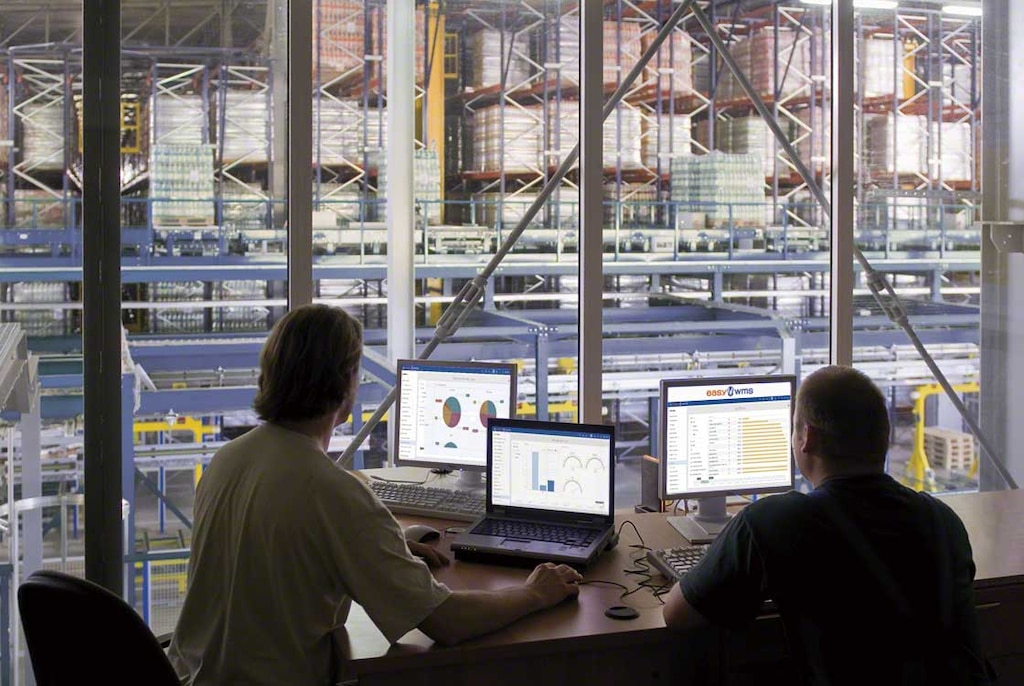
L'amélioration continue comme gage de compétitivité
Dans un contexte où la logistique ne cesse d'évoluer, avec des technologies qui vont potentiellement révolutionner le quotidien des entreprises dans un avenir proche, il est essentiel d’introduire des stratégies d’améliorations continues afin de rester compétitif.
Le premier pas vers une chaîne logistique performante consiste à contrôler et analyser les KPI de votre entrepôt dans le but d'identifier les défaillances et de se débarrasser des processus ne créant pas de valeur ajoutée. La mise en œuvre d'une stratégie d'amélioration continue dans votre entreprise est le seul moyen de réduire les coûts logistiques et d'optimiser vos ressources.
Vous souhaitez maximiser la performance de votre entrepôt, n'hésitez pas à nous contacter, un de nos experts vous aidera à tirer le meilleur parti de votre logistique.