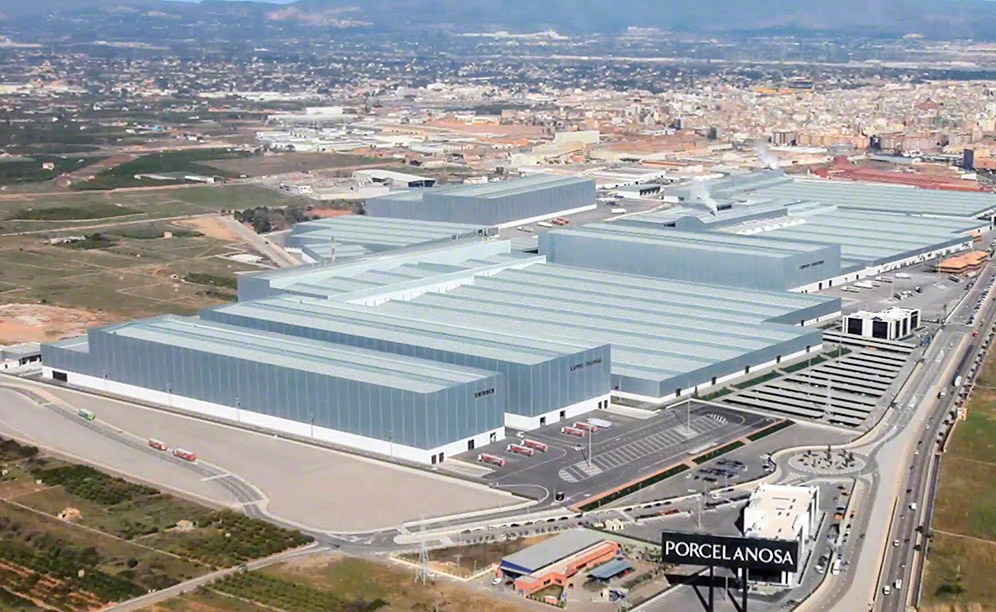
Les cinq centres logistiques du groupe Porcelanosa offrent une capacité de stockage de plus de 275 000 palettes et de 15 000 caisses
Le groupe Porcelanosa et Mecalux : une relation de confiance, de croissance et de succès de longue date
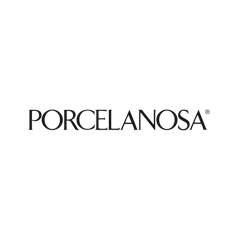
Le complexe logistique du groupe Porcelanosa situé à Vila-real (Espagne) est composé de cinq centres logistiques avec des entrepôts automatisés à grande capacité. L’entreprise, qui se distingue par sa constante innovation, a incorporé les toutes dernières technologies à ses processus logistiques, ce qui l'a aidée à se développer et à renforcer son leadership au niveau international. Mecalux a conçu et mis en place des solutions de stockage performantes et adaptées à ses besoins. Pour faire face à l'évolution du marché, les centres ont été conçus de façon à pouvoir être développés afin d’augmenter leur surface de stockage, sans interrompre les opérations.
À propos du groupe Porcelanosa
Le groupe Porcelanosa est l’un des groupes d’entreprises espagnols les plus importants jouissant d’une forte notoriété au niveau mondial. Il a été fondé en 1973 dans la ville de Vila-real (à 70 km de Valence), avec une vocation internationale incontestable. À l’heure actuelle, il est présent dans près de 150 pays.
Initialement, le groupe Porcelanosa se consacrait à la fabrication de céramiques, la diversification de ses produits et services a été capital afin de renforcer sa croissance. Aujourd’hui, il offre une vaste gamme de revêtements naturels, de céramique, de façades ventilées, de mobilier de cuisine, de sanitaires, de robinetteries et de solutions constructives pour l'architecture contemporaine.
Huit entreprises forment le groupe : Porcelanosa, Venis, Gamadecor, Systempool, L’Antic Colonial, Butech, Noken et Urbatek.
Cinq entrepôts automatisés
Les centres logistiques de l'entreprise situés à Vila-real jouissent d'un emplacement idéal pour la distribution rapide de leurs produits sur l’ensemble du territoire espagnol et dans le monde entier.
En 2003, Mecalux a construit le premier entrepôt automatisé du groupe Porcelanosa. En tenant compte des exigences exposées, des prévisions de croissance et de la stratégie de l’entreprise, Mecalux a envisagé la possibilité de construire des entrepôts différents pour Porcelanosa, Venis, L’Antic Colonial, Noken et Urbatek. Ce projet de grande envergure s'est étalé sur 10 ans.
L’équipe technique de Mecalux a travaillé conjointement avec celle du groupe Porcelanosa, afin de concevoir la meilleure solution pour répondre à leurs besoins logistiques. Il en résulte un modèle d'entrepôt automatisé qui est valable pour chacune des entreprises du groupe (adapté aux différentes tailles, volumes et rotations des produits).
L'approche se distingue par sa simplicité : l'entrepôt est composé de transstockeurs qui effectuent l'entrée et la sortie automatique de la marchandise, tandis que la réception, l'expédition et le picking sont effectués dans la zone périphérique à l'aide d'un circuit complet de convoyeurs et de navettes.
Grâce à ce type de solution, le groupe Porcelanosa a pu atteindre la productivité souhaitée dans chacun de ses centres, tout en proposant un service rapide et efficace. Dans la pratique, la seule chose qui différencie les entrepôts entre eux est leur capacité de stockage, leur fonctionnement restant très similaire.
Mecalux et le groupe Porcelanosa
Les deux sociétés ont tissé une étroite collaboration depuis les années 1980. L’histoire du groupe Porcelanosa et de Mecalux a suivi une trajectoire très similaire : les deux entreprises basent leur croissance sur le développement technologique et sont toutes les deux équipées d'un vaste réseau de distribution international.
Mecalux a équipé les entrepôts régionaux et les centres de distribution du groupe, en Europe et sur le continent américain.
Les premiers entrepôts ne disposaient ni du degré d’automatisation ni de la sophistication actuelle. Les bâtiments étaient bas et les opérateurs utilisaient des engins de manutention pour la manipulation des palettes. De plus, la préparation des commandes respectait le principe de l'« homme vers le produit ». Néanmoins, la forte croissance que l’entreprise a connue en Espagne a suscité le besoin de construire plus d’entrepôts, plus hauts et ayant une plus grande capacité de stockage. Pour obtenir une meilleure productivité, une étape supplémentaire vers l'automatisation de la gestion devait être franchie, menant par la suite, vers l'automatisation de toutes les opérations.
Les centres logistiques situés à Vila-real
Tous les centres logistiques du groupe Porcelanosa se trouvent sur une vaste parcelle de terrain. Les distances parcourues représentant un coût de manutention élevé au moment de transporter la marchandise, ce coût devait être minimisé. Mecalux a proposé que les entrepôts soit les plus proches possible des sorties de production. De même, la communication entre les deux zones a été réalisée à travers des tunnels avec des convoyeurs automatiques, pour éviter les mouvements permanents de chariots élévateurs.
La réalisation des différents projets a été progressive. Le premier entrepôt construit a été celui de Porcelanosa, mis en fonctionnement en 2003, suivi de celui d'Urbatek, en 2007. Puis, furent érigés les entrepôts de L’Antic Colonial, de Noken, et enfin celui de Venis en 2011.
Une partie importante de l'approvisionnement des entrepôts d'Urbatek et de L’Antic Colonial provient de l’extérieur de l'usine, c’est pourquoi ils sont situés à l'une des extrémités du centre logistique. Pour sa part, l'entrepôt de Noken se trouve dans la même commune dans un bâtiment à proximité du siège principal.
Sur les cinq entrepôts, quatre sont très similaires (entrepôts automatisés pour palettes) et seul celui de Noken (entrepôt automatisé pour caisses) se démarque considérablement des autres. Pour pouvoir comprendre leur fonctionnement, trois des cinq entrepôts automatisés du groupe Porcelanosa sont décrits ci-après.
L'entrepôt de Venis
Créée en 1986, Venis produit des planchers et des revêtements céramiques aux formats, types et finitions très variés. Il se distingue par la polyvalence de sa conception et l’utilisation de la technologie la plus avancée pour la fabrication de carreaux de faïence et de grès porcelainé.
L'entrepôt automatisé est construit à l’intérieur d’un bâtiment de 35 m de haut et occupe une surface totale de 25 000 m2. Toutefois, 8 000 m2 sont occupés pour le stockage, l'espace restant étant réservé pour un agrandissement futur.
Cet entrepôt est séparé de l’usine de fabrication. La communication entre les deux centres est automatique et s'effectue à travers un tunnel souterrain formé par des convoyeurs et des élévateurs.
L’entrepôt se compose de dix allées de stockage, avec des rayonnages à simple profondeur, de part et d'autre de chaque allée circule un transstockeur. À l’extrémité des allées, il y a deux niveaux de transport : les entrées sont effectuées au niveau supérieur et les sorties au niveau inférieur. Au total, huit élévateurs relient les deux étages, afin d'atteindre le flux de mouvements requis. Il existe une entrée directe pour la marchandise provenant de la production et deux entrées auxiliaires qui introduisent, soit les palettes provenant d’autres centres, soit les palettes vides. Dans tous les cas, les palettes doivent passer par un contrôle de qualité rigoureux avant d'entrer dans l’entrepôt.
Le picking constitue l’opération de fonctionnement fondamentale de cet entrepôt. Un grand nombre de commandes y sont préparées chaque jour. C'est pourquoi une vaste zone de picking a été prévue en face des allées de stockage.
Entrée dans l’entrepôt
L’installation commence par la sortie des lignes de production. Les convoyeurs à rouleaux du tunnel souterrain transportent automatiquement la marchandise jusqu'à l'entrepôt.
Au début comme à la fin du tunnel, il y a des élévateurs qui acheminent les palettes jusqu’au niveau correspondant. Une fois que les palettes sont arrivées dans l'entrepôt, deux élévateurs se chargent de monter la marchandise jusqu’à l’étage supérieur. Chacun d'entre eux est capable de transporter deux palettes pouvant peser jusqu'à 1 600 kg.
Les élévateurs disposent d’éléments de sécurité comme des clôtures, des barrières optiques, des portes d'accès sécurisées pour la maintenance et des portes rapides automatiques pour le passage des palettes. À l'étage supérieur, a été installé le circuit de convoyeurs d’entrée dans l’entrepôt. Il intègre une recirculation pour distribuer facilement les palettes sur une ligne en cas de problème. En même temps, il communique avec les autres élévateurs qui montent les palettes provenant de la zone de picking et des entrées auxiliaires.
Les entrées auxiliaires sont situées sur l'un des côtés de l’entrepôt et sont destinées aux produits provenant de l'extérieur et aux palettes vides qui ont été générées pendant le picking. Les palettes vides sont empilées et introduites dans le compacteur afin de garantir leur stabilité et leurs dimensions avant d'entrer dans l'entrepôt.
Caractéristiques de l'entrepôt
L'entrepôt mesure 160 m de long et 31 m de haut. Il est composé de dix allées avec des rayonnages à simple profondeur de part et d'autre et 23 niveaux contenant chacun deux palettes. Au total, la capacité de stockage obtenue s'élève à 65 320 palettes de 800 x 1 200 mm, d’une hauteur maximale de 1 450 mm et d’un poids admissible maximum de 1 600 kg.
Les transstockeurs bicolonnes travaillent à une vitesse de translation de 180 m/min, effectuant un total de 237 cycles combinés par heure. L'utilisation de ces engins permet d'obtenir un flux de mouvements très élevé sans intervention d'opérateur, ce qui supprime toute erreur logistique provenant de la gestion manuelle. Les transstockeurs, équipés d'un récupérateur d’énergie, sont capables de recueillir et de renvoyer au réseau électrique environ 15 % de l'énergie générée pendant les manœuvres de descente de la nacelle et de décélération de l’axe de déplacement.
Zone de picking
Elle a été installée au niveau inférieur, juste derrière le circuit de convoyeurs de sortie et en face des allées de stockage. Elle est formée par huit postes de picking alignés, où peuvent être préparées simultanément jusqu’à 32 commandes.
Chaque poste de picking dispose d'une zone d’accumulation pour les palettes qui sont utilisées dans les opérations et transportées jusqu’aux postes de picking au moment voulu. Conjointement, le circuit de recirculation permet de séquencer la pose de la marchandise dans la palette, en suivant des critères de capacité d'empilement.
Pour faciliter les manœuvres des opérateurs, chaque poste dispose d'un bras mécanique qui soulève les paquets les plus lourds avec un minimum d'efforts.
Les tables de préparation des palettes d’origine (où sont récupérés les produits composant les commandes) et celles de destination (où sont déposés les articles) s'élèvent au moyen d'un système hydraulique disposant la palette dans une position ergonomique.
D’autres part, quatre élévateurs ont été installés pour envoyer les palettes avec les produits restants à l’étage supérieur, afin de les faire entrer à nouveau dans l’entrepôt. Il y a deux navettes doubles qui gèrent les palettes vides et les commandes terminées. Ces dernières passent par le poste de filmage et, sont réparties en deux canaux de préchargement avant leur expédition.
Un tunnel de communication piéton relie la zone de picking au reste de l’entrepôt. Il traverse la partie inférieure de l’allée des navettes et des convoyeurs des postes de picking.
Communication
Le fait d'avoir séparé les entrées des sorties en deux étages évite les interférences entre les deux types d’opérations. Le mouvement est continu : les entrées et les sorties de chaque allée sont fluides.
Une vaste zone de préchargement, dans laquelle les palettes sont préparées pour l’expédition, a été aménagée. La marchandise consolidée est accumulée dans cette zone. Elle est ensuite transportée par des véhicules de répartition et de transport.
Il y a deux blocs de préchargement (1 et 2) avec six canaux pour accumuler les palettes. Ce système réduit considérablement le temps consacré au chargement des camions.
L’entrepôt de L’Antic Colonial
La variété de produits disponibles a induit des exigences spécifiques dans certains des entrepôts du groupe. Tel est le cas de L’Antic Colonial, entreprise fabricante de revêtements pour le sol et les murs, qui travaille avec des colis plats de grandes dimensions (revêtements de parquets) sur des palettes de 2 440 x 1 200 mm.
Mecalux a conçu sur mesure tous les engins de manutention pour orienter ces produits et les placer correctement sur les niveaux qui leur sont assignés. Sont installés deux engins de chaque type : transstockeurs, convoyeurs, élévateurs, et navettes. Il y a également deux zones de picking.
En plus des postes de picking, une zone indépendante située perpendiculairement aux allées où sont stockés les produits de grandes dimensions, a été aménagée pour préparer les commandes contenant ce type de produits spécifiques. Les convoyeurs et la navette se chargent de relier l'entrepôt avec les postes de picking.
L'entrepôt de Noken
D'autre part, Noken, entreprise spécialisée dans l’équipement de salles de bain, a construit un magasin automatique à caisses miniload (au lieu d’un entrepôt pour palettes). Ce choix a été fait en raison de la taille et du poids des articles à stocker, composés principalement de robinetteries et d'accessoires pour salle de bain.
L’entrepôt est composé de deux allées de 70 m de long, dotées, de chaque côté de rayonnages à simple profondeur. Elles mesurent 15 m de haut et comprennent 30 niveaux fournissant une capacité de stockage de 15 360 caisses. Dans cet entrepôt, se trouvent deux modèles de caisses différentes : d'une part, des caisses de 600 x 400 x 420 mm, et d'autre part, des caisses de 600 x 400 x 120 mm, d'un poids unitaire maximal de 50 kg.
Dans chacune des allées circule un trans-stockeur effectuant automatiquement les entrées et les sorties de la marchandise. Dans la partie frontale de l'entrepôt, il y a un circuit de convoyeurs qui relie les allées de stockage à deux postes de picking et à un poste de réapprovisionnement.
Les convoyeurs comme les postes de picking ont été spécifiquement conçus pour fonctionner avec les deux modèles de caisses.
Les transstockeurs fournissent la marchandise aux postes de picking, les opérateurs en extraient les articles et les incluent dans la commande correspondante. Les dispositifs put-to-light indiquent la caisse dans laquelle les articles doivent être introduits, les opérateurs confirment qu'ils ont exécuté l’action en appuyant sur un indicateur. Les commandes sont préparées par vagues : les opérateurs préparent plusieurs commandes simultanément.
Easy WMS et Galileo
Les cinq entrepôts du groupe Porcelanosa sont pilotés par le logiciel de gestion d'entrepôt Easy WMS de Mecalux. Celui-ci coordonne et pilote toutes les opérations, de la réception de la marchandise (en identifiant et en validant les produits et leurs provenances) en passant par le stockage (en fonction des critères de consommation et de rotation des produits) jusqu’à la préparation et expédition des commandes (en regroupant les palettes en fonction de leur contenu ou de leur destination).
Easy WMS de Mecalux est capable d'améliorer la qualité du service du groupe Porcelanosa et de permettre des économies de coûts en augmentant la productivité de l’entrepôt. De même, il s'agit d'un système évolutif, qui peut augmenter ou réduire les ressources et la puissance en fonction des exigences de la société.
Les entrepôts du groupe Porcelanosa étant automatisés, le logiciel de commande Galileo de Mecalux, a été installé afin de diriger les déplacements de tous les engins de manutention pour effectuer les tâches de transport et de stockage (transstockeurs, convoyeurs, élévateurs et navettes).
Garantie d'avenir
Le groupe Porcelanosa, leader mondial dans son secteur, a incorporé les dernières technologies dans tous ses processus logistiques. Mecalux a contribué à la croissance du groupe au fil des ans, grâce à la conception et à l'équipement de ces entrepôts.
Ces entrepôts répondent pleinement aux besoins exprimés initialement par le groupe Porcelanosa. Ils offrent une grande capacité de stockage, disposent d'engins de manutention très modernes et dont le fonctionnement est très souple et efficace.
Les centres logistiques de Vila-real ont été conçus afin de pouvoir se développer dans le futur, lorsque la demande du marché le requerra. Ils pourront dès lors augmenter la capacité de stockage, agrandir le circuit de convoyeurs et ajouter davantage de postes de picking, le tout sans interrompre les opérations.
À son tour, le logiciel Easy WMS de Mecalux accompagnera l’entreprise à tout moment, en s'adaptant aux changements, aux nouveaux besoins et à l'éventuelle croissance de la production du groupe.
Ces dernières années, l’entreprise a connu une croissance sans précédent et a renforcé son leadership dans le monde entier. Avec la collaboration de Mecalux, elle a pu profiter des avantages que représente l'automatisation de ses entrepôts et relever le défi d’augmenter au maximum sa productivité.
L'entrepôt de Venis | |
---|---|
Année de construction: | 2011 |
Surface de stockage: | 8.000 m² |
Capacité de stockage: | 65.000 palets |
Nb. de transstockeurs: | 10 |
Hauteur de l’entrepôt: | 31 m |
Galerie
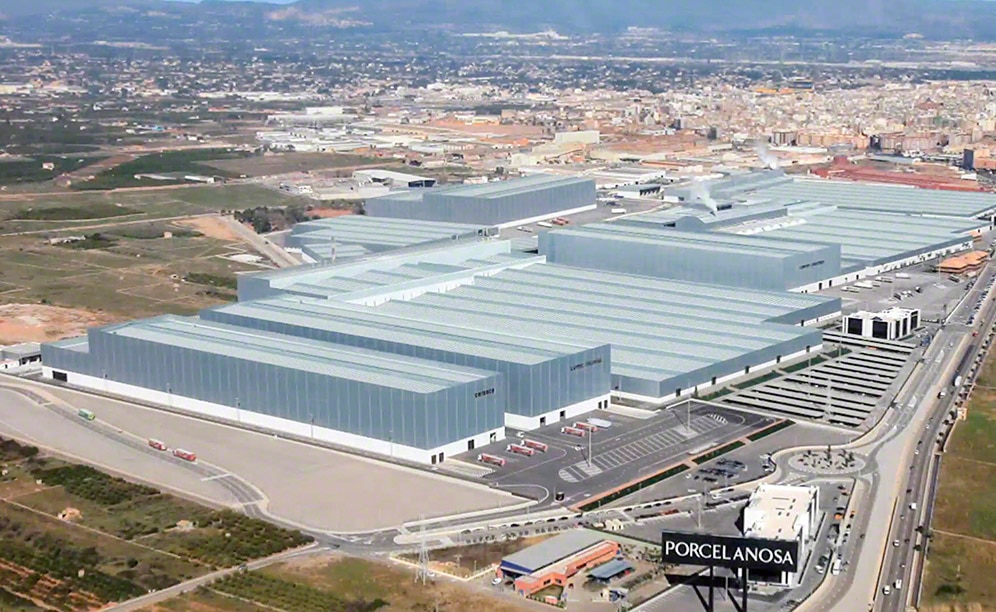
Le complexe logistique du groupe Porcelanosa est composé de cinq centres logistiques avec des entrepôts automatisés à grande capacité
Demandez conseil à un expert